Introduction
In the race toward cleaner and more sustainable energy solutions, PEM fuel cells (Proton Exchange Membrane fuel cells) have emerged as a frontrunner. These high-efficiency, zero-emission devices hold promise for revolutionizing energy across sectors—from transportation to portable electronics and stationary power systems.
But while their environmental appeal is well-publicized, one crucial question remains: How efficient are PEM fuel cells, really? In practical applications, efficiency becomes the defining metric of their feasibility and long-term adoption.
This guide provides a deep dive into PEM fuel cell efficiency, exploring the key variables that govern their performance, how they compare with other energy technologies, and where the industry is heading in terms of innovation and optimization.
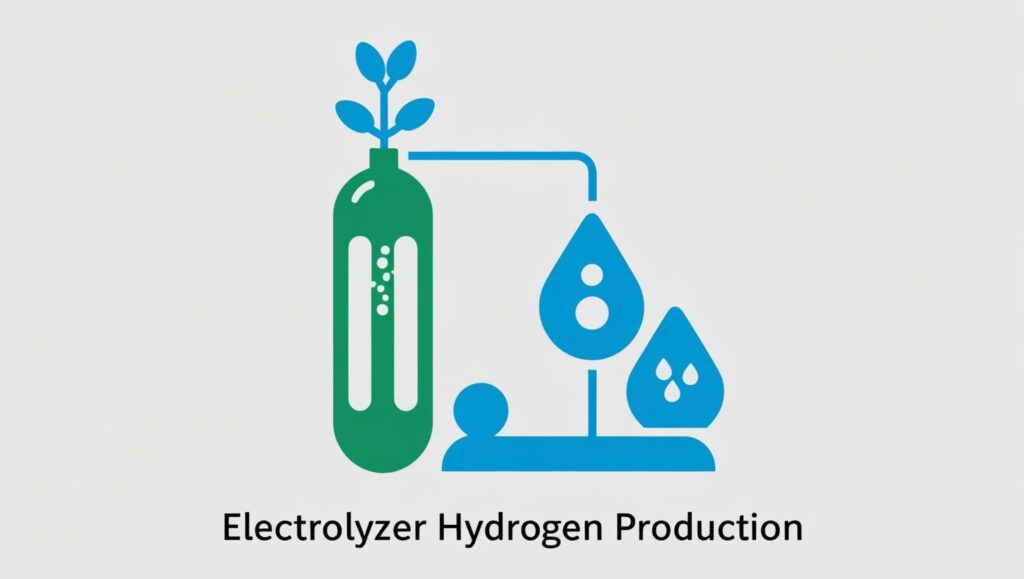
What are PEM Fuel Cells? (A Brief Overview)
PEM fuel cells work by converting chemical energy from hydrogen into electrical energy through an electrochemical reaction with oxygen. The key differentiator from combustion-based engines is that this process happens without burning fuel—resulting in a clean emission profile where the only byproduct is water.
Core Components of a PEM Fuel Cell
- Membrane: The heart of the PEM cell, usually made of Nafion, allows protons to pass while blocking electrons and gases.
- Electrodes: Porous layers coated with a catalyst where reactions occur.
- Catalyst Layer: Typically platinum-based, it accelerates the splitting of hydrogen into protons and electrons.
- Bipolar Plates: Distribute gases evenly and collect current.
This structure supports efficient electron flow and proton conduction, maximizing energy output from each hydrogen molecule introduced into the system.
Defining Efficiency: Understanding the Metrics
When discussing PEM fuel cell efficiency, it’s vital to distinguish between several key metrics:
Voltage Efficiency
This measures the ratio of actual voltage output to the theoretical maximum. Losses due to resistance, activation, and concentration result in typical voltages of 0.6–0.7V compared to the ideal 1.23V.
Faradaic Efficiency
This metric determines how effectively the transferred charge results in chemical conversion. Ideally, it approaches 100%, meaning nearly all electrons contribute to productive reactions.
Fuel Utilization Efficiency
Assesses how much of the input hydrogen is used in generating power versus what’s vented unused. Efficient systems aim for 80–90% fuel utilization.
Overall System Efficiency
Combines thermal, electrical, and mechanical losses across the system. In practical deployments, this ranges from 40% to 60%, depending on the application and configuration.
Understanding these metrics allows engineers and stakeholders to assess trade-offs and identify areas for performance improvements.
Factors Affecting PEM Fuel Cell Efficiency
A. Operating Conditions
- Temperature: PEM fuel cells typically operate best at 60–80°C. Too low, and reaction rates drop; too high, and membranes degrade.
- Pressure: Higher pressures improve gas solubility and reduce concentration losses, enhancing performance.
- Humidity: Essential for membrane conductivity. Dry membranes reduce ion transfer; overhydration causes flooding.
- Flow Rates: Stoichiometric ratios of hydrogen and oxygen must be optimized to avoid inefficiencies and gas starvation.
B. Materials and Design
- Membrane: Thinner membranes reduce resistance but may compromise durability. Advances include composite and hydrocarbon membranes.
- Electrodes: High surface area catalysts improve efficiency. Nanostructured catalysts are emerging as high-performance options.
- Bipolar Plates: Channels must ensure uniform gas distribution and effective water management. Designs like serpentine or interdigitated flow fields help optimize.
C. Fuel Quality and Purity
- Impurities: Carbon monoxide can poison platinum catalysts, drastically reducing efficiency. Hydrogen purity must exceed 99.99%.
- Processing Techniques: Technologies like PSA (Pressure Swing Adsorption) and reforming ensure high-quality hydrogen delivery.
Continuing the long-form article on:
Unlocking PEM Fuel Cell Efficiency: The Ultimate Performance Guide
Real-World PEM Fuel Cell Efficiency: What to Expect
When translating laboratory performance to real-world applications, PEM fuel cell efficiency depends significantly on the use case and system integration.
1. Stationary Power Generation
PEM fuel cells used in stationary applications—such as backup power or distributed energy systems—tend to achieve efficiency levels between 40% and 50%. These setups benefit from stable operating conditions and better system controls. When integrated with combined heat and power (CHP) systems, total efficiency (electrical + thermal) can exceed 80%.
2. Transportation (Fuel Cell Vehicles)
Fuel cell electric vehicles (FCEVs), like the Toyota Mirai or Hyundai Nexo, typically achieve net efficiencies around 50–60% during regular driving. However, efficiency fluctuates due to:
- Variable load demands
- Dynamic operating temperatures
- Regenerative braking systems
Despite these variations, FCEVs generally outperform internal combustion engines, which have average efficiencies of just 20–30%.
3. Portable Power Devices
Compact PEM fuel cells designed for military or remote use provide on-demand power where conventional grids are unavailable. Efficiency here can be around 30–50%, constrained by miniaturization and environmental challenges like temperature fluctuations and limited fuel availability.
4. Comparative Efficiency Overview
Technology | Typical Efficiency |
---|---|
PEM Fuel Cells | 40–60% |
Internal Combustion Engines | 20–30% |
Lithium-Ion Batteries | 90–95% (charge/discharge) |
Solid Oxide Fuel Cells (SOFCs) | 45–65% (higher with CHP) |
This comparison shows that while batteries offer higher immediate efficiency, PEM fuel cells excel in scalability, refueling speed, and range, especially where long-duration and high-power output are needed.
Improving PEM Fuel Cell Efficiency: Current Research and Future Trends
1. Advanced Membrane Materials
Newer hydrocarbon-based membranes offer lower cost and enhanced conductivity compared to traditional perfluorosulfonic acid membranes (e.g., Nafion). These membranes also improve thermal stability and reduce gas crossover, a major source of energy loss.
2. Novel Catalyst Designs
Catalyst research is pivoting toward non-platinum group metals (non-PGMs) to lower costs while maintaining high electrochemical activity. Promising developments include:
- Iron-nitrogen-carbon (Fe-N-C) catalysts
- Core-shell nanoparticles
- Durable platinum-alloy catalysts with increased surface area
3. Optimized Flow Field and Stack Design
Innovations in 3D-printed flow fields and multi-scale modeling are enabling superior gas distribution, improved water management, and minimized pressure drop across the stack—leading to measurable performance boosts.
4. Hybrid Energy Integration
PEM fuel cells are increasingly being integrated with:
- Renewable sources like solar and wind for grid stabilization.
- Battery systems in hybrid vehicles to balance peak loads and extend driving range.
These integrations maximize system-level efficiency while compensating for intermittent power demands and enhancing energy resilience.
Challenges and Limitations
While the potential of PEM fuel cells is undeniable, several roadblocks must be addressed to realize their full efficiency and commercial scalability:
1. Cost of Materials and Manufacturing
- Platinum-based catalysts and fluorinated membranes contribute to high upfront costs.
- Manufacturing techniques need further streamlining to reduce costs at scale.
2. Durability and Degradation
- Catalyst sintering and membrane thinning limit long-term performance.
- Current PEM stacks typically last 5,000–8,000 hours for vehicles, compared to over 100,000 hours for internal combustion engines.
3. Hydrogen Infrastructure
- Hydrogen production, storage, and distribution systems remain underdeveloped.
- Green hydrogen (via electrolysis using renewable energy) is promising but expensive.
4. Policy and Regulatory Support
- Standardization of testing and certification.
- Incentives for fuel cell adoption in public and private sectors.
Overcoming these challenges requires a combination of policy frameworks, technological breakthroughs, and industry collaboration.
FAQs on PEM Fuel Cell Efficiency
1. What is the typical efficiency range of a PEM fuel cell?
PEM fuel cells operate at 40–60% electrical efficiency, depending on system design and operating conditions. When used in CHP systems, total efficiency can reach up to 80%.
2. How do impurities affect PEM fuel cell efficiency?
Impurities like carbon monoxide (CO) in hydrogen fuel can poison the catalyst, drastically reducing its activity and lowering efficiency. High-purity hydrogen and filtration systems are essential.
3. Are PEM fuel cells more efficient than batteries?
While batteries have higher charge-discharge efficiency (up to 95%), PEM fuel cells offer advantages in energy density, range, and quick refueling, especially in transportation and grid applications.
4. What maintenance practices improve fuel cell efficiency?
Regular checks on membrane hydration, gas flow rates, and catalyst health help maintain optimal performance. Avoiding contaminants is key to sustaining long-term efficiency.
5. How does operating temperature influence efficiency?
PEM fuel cells perform best at 60–80°C. Too low, and reaction rates drop; too high, and membranes may degrade. Proper thermal management ensures efficient operation.
6. What innovations are improving PEM fuel cell efficiency?
Advancements in catalyst engineering, membrane technology, and flow field designs, as well as integration with renewable energy systems, are driving significant efficiency gains.
Conclusion
PEM fuel cells stand at the forefront of clean energy technology, offering a balance of efficiency, scalability, and sustainability. Their performance hinges on a complex interplay of factors—from materials and design to operating conditions and fuel quality.
With ongoing research into cost-effective materials, advanced catalysts, and hybrid integration models, PEM fuel cells are steadily evolving into more viable and efficient alternatives to conventional energy systems.
🌱 Ready to elevate your energy solutions? Contact us today to explore how our PEM fuel cell systems can boost your project’s efficiency and reduce its environmental footprint. Get a free consultation now!